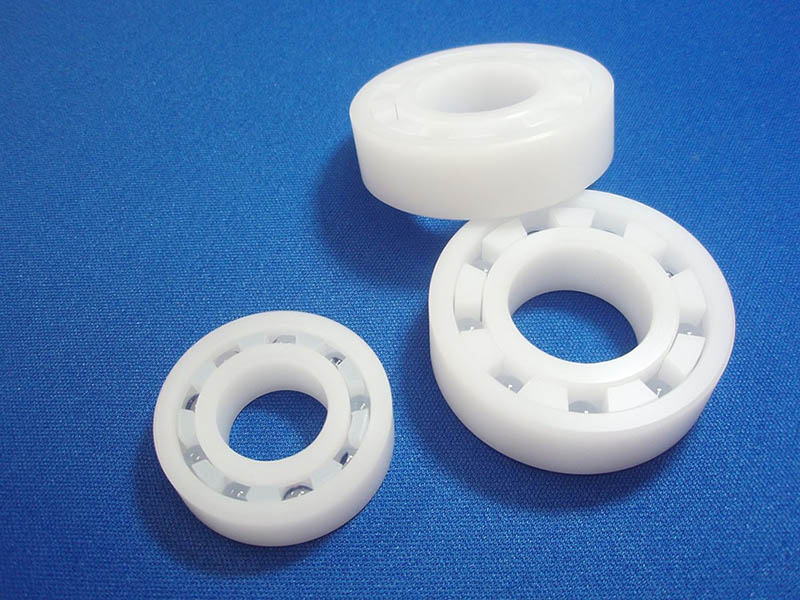
POM Material Injection Molding
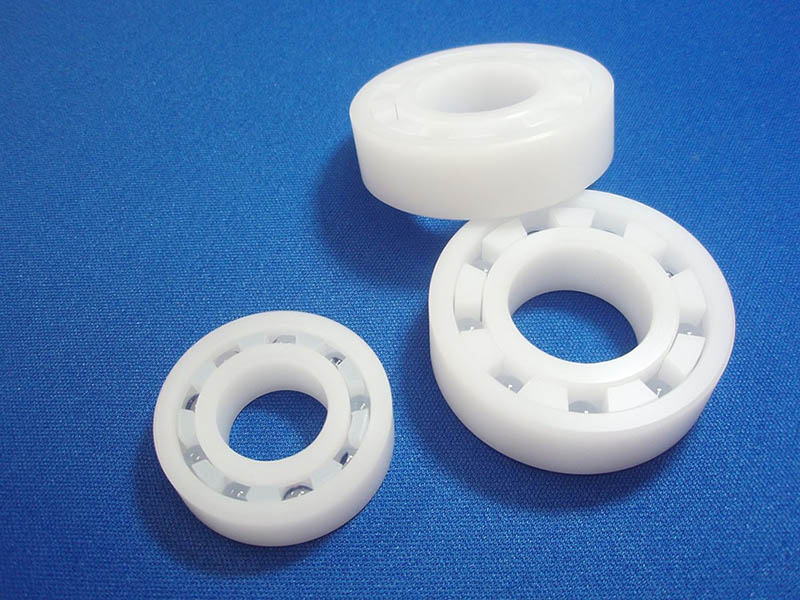
Polyoxymethylene (POM) is a thermoplastic material also known as acetal. POM-H (polyoxymethylene homopolymer), POM-K (polyoxymethylene copolymer) is a high density, high crystallinity thermoplastic engineering plastic with good physical, mechanical and chemical properties, especially with excellent friction resistance.
POM is a crystalline plastic with a sharp melting point. Once the melting point is reached, the melt viscosity drops rapidly. Decomposition occurs when the
temperature exceeds a certain limit or the melt is heated for too long.
Copper is a POM degradation catalyst. Copper should be avoided where it is in contact with the POM melt.
1. Plastic processing
POM has a small water absorption, generally 0.2%-0.5%. Under normal circumstances, POM can be processed without drying, but it must be dried for wet
materials. The drying temperature is above 80℃ and the time is more than 2 hours. The specific conditions should be based on the supplier’s data.
The proportion of recycled materials used is generally not more than 20-30%. However, depending on the type of product and the end use, it can sometimes be up to 100%.
2. The selection of plastic machine
In addition to the requirement that the screw has no stagnant area, the POM has no special requirements for the injection molding machine, and generally
can be injection molded.
3. Mold and gate design
The common mold temperature is controlled to 80-90℃, the runner diameter is 3-6 mm, the gate length is 0.5 mm. The gate size depends on the thickness
of the wall, and the circular gate diameter should be at least 0.5-0.6 times the thickness of the product. The width of the rectangular gate is usually 2 times
or more of the thickness, the depth is 0.6 times the wall thickness, and the draft angle is between 40′-1º30′.
Exhaust system
POM-H thickness 0.01-0.02mm width 3mm
POM-K thickness 0.04mm width 3mm
4. Melting temperature
POM-H can be set to 215℃ (190℃ – 230℃)
POM-K can be set to 205℃ (190℃ – 210℃)
5. Injection speed
Medium speed. If too slow, it produces ripples. If too fast, it is easy to produce grain and shear overheating.
6. Back pressure
The lower the better, generally no more than 200bar
7. Stay time in barrel
POM-H can be held at 215℃ for 35 minutes
POM-K can stay in 205℃ for 20 minutes without decomposition.
POM-K can be retained for 7 minutes at 240℃. If the machine is shut down, the barrel temperature should be lowered to 150℃. If you want to stop for a
long time, you must clean the machine and turn off the heater.
8. After machine stops
The cleaning barrel must use PE or PP. Turn off the heating and push the screw in the front position. The barrel and screw must be kept clean. Impurities or dirt can change the thermal stability of the POM (especially POM-H).
9. Post processing
For very warm parts and high quality requirements, heat treatment is required.
The annealing treatment effect can be carried out by immersing the product in a hydrochloric acid solution having a concentration of 30% for 30 minutes,
and then visually discriminating whether cracks have residual stress.